How to Repair a Joist
Odds are that the joists in an old home have suffered considerable damage
over the years. Perhaps a small crack formed into a bigger one, or maybe
someone cut into a joist for reasons that seemed reasonable at the time.
Damaged joists, regardless of the cause, must be repaired before a new
ceiling is installed. Not all cracks compromise the strength of the joist;
however, if the joist is sagging or if the crack runs clear to the bottom
edge of the joist, it must be repaired. Only in rare cases is it best
to remove a joist, even if it’s seriously damaged. Keep in mind that
the floor sheathing is nailed into the floor joists, so pulling a joist
risks damaging the finished floor above. An existing joist may be reinforced and repaired by attaching a same-sized
joist alongside it; this is called “sistering.” The new lumber must be
as long as the existing joist and of the same depth, and it’s supported
in the same locations. Maneuver the new joist into position (cutting
off one corner of the joist may help), push the old joist back where
it belongs, and then use 16d nails to nail the two together.
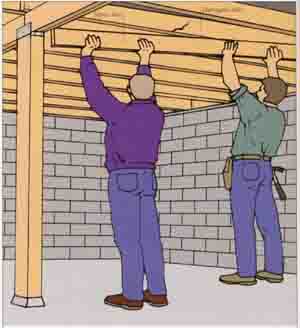
Figure 20: A piece of lumber that’s attached to the side of a joist
to strengthen it’s called a “sister.” It should be almost the same length and exactly the same depth as the joist it supports. Cutting off the
corner of opposite edges of the joist can help put it into position.
Reducing Moisture
A basement can’t be turned into a livable space unless it’s guaranteed
to stay dry. Water problems range in seriousness from mild condensation and seepage to periodic flooding. Given enough time and money, all water
problems can be solved, but that doesn’t mean the effort is justified.
How to Determine the Source of Water or Moisture
Assuming that the plumbing doesn’t leak, basement moisture comes either
from seepage (water from out side the house leaking through walls or
floor) or from condensation (the result of warm, moist air hitting a
cold masonry wall or cold water pipes). The source of the water may be
identified by conducting a simple test. If condensation is the problem,
get rid of it by either installing a dehumidifier in the basement or
insulating the walls and water pipes.
Seeping water is harder to get rid of because it might be coming from
any or all of these sources:
Gutters: Those that don’t direct water away from
the foundation are a problem. Clogged gutters let water spill over and run down the siding toward the foundation wall. Leaders that dump water
near the foundation encourage water to soak in at exactly the wrong places.
Use splash blocks or leader extensions to direct water away from the
house.
Poor Grading: If the grading slopes toward the house
or allows water to pool near the foundation, it’s a problem. To conduct
water away from the foundation, the grade must drop at least 6 inches
in 10 feet all around the house. Fill in pockets that encourage water
to pool.
No Footing Drains: Some water inevitably reaches the
bottom of the foundation but it won’t be a problem if perforated pipes,
known as “footing drains”, lead it away. Most newer homes have footing
drains but older houses might not. Drains can be added to older houses,
though not without quite a bit of effort. A contractor is need here.
It requires the use of heavy equipment to excavate the entire perimeter
of the foundation. It also involves placing gravel sub-drains; installing
perforated piping for the main drains, and lastly, backfilling and re-grading.
Cracked Foundation Walls: Water will ultimately get
through even the smallest cracks -- use hydraulic cement to patch all
cracks.
Pipes / Electrical Lines: The problem isn’t the pipe
or the line; it’s the gap (channel) around the pipe and the
line that leads water into the basement. Seal gaps with hydraulic cement
or silicone sealant (a high-performance product similar to silicone caulk).
Badly-Waterproofed Foundation: A foundation such as
this allows moisture to migrate directly through the masonry. Concrete and concrete block are not waterproof. The outside of every foundation
wall is supposed to be waterproofed before backfilling. If the
foundation wasn’t waterproofed or if the waterproofing failed, the solution
isn’t something for the beginner. Similar to installing new footing drains,
extensive excavation is usually required.
Proximity Vegetation: Plants retain moisture in the
soil, and their shade reduces the evaporation of ground moisture. Both
factors add to water problems. Also: plants that require a lot of deep
watering add moisture to the soil that could seep in.
High Water Table: The water table varies in depth from
area to area and even from season to season. Not much can be done about
the level, but foundation drains and sump pumps can help conduct water
away before it becomes a problem.
Sealing a Masonry Wall
Even if the basement isn’t to the types of water issues that present
themselves as active drips, moisture might still be seeping through the
masonry itself. This kind of moisture movement can be halted by sealing
the walls from inside the basement. Even if the walls appear “dry,” sealing
them is a wise precaution. After all, it does not take much moisture
to warp wood paneling or to encourage a musty smell. To seal the walls,
brush them with a product that contains portland cement and synthetic
rubber. This product goes by many names: cement paint, waterproofing
paint, basement paint, or basement waterproofer. Though some brands claim
to keep out water that's under a modest amount of pressure, nothing
applied to the inside of the walls can solve serious water problems.
After applying a waterproofing paint, paint over it with a quality latex
paint.
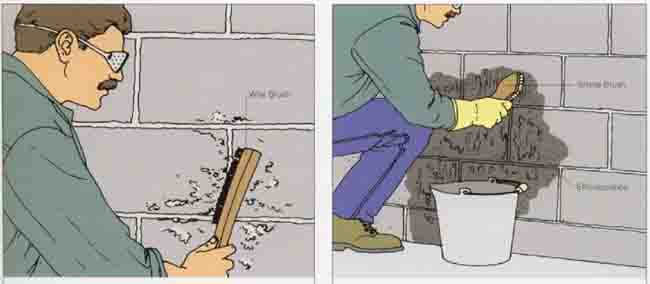
1. Use a scraper and a wire brush to remove loose mortar and dirt, and then vacuum the wall to remove the remaining dust and debris. 2.
Use a bristle brush and a mixture of etching compound and water to remove
efflorescence on the surface of the masonry. Wear rubber gloves and eye
protection.
1. Cleaning the Surfaces. Use a wire brush to remove loose
mortar and dirt from the walls. Sealing is most effective on a wall that
has never been painted, but if all of the old paint is removed, the sealant
still has a chance to do its job.
2. Removing Efflorescence. A harmless, white, crystalline deposit
called efflorescence some times forms on concrete or concrete- block
walls. It’s caused by water- soluble salts within the masonry that migrate
to the wall’s surface and interferes with the bond between the and then
use a trowel to force the cement mixture into cracks and holes. Use the
trowel to smooth out patched areas immediately.
5. Plugging Other Water Problems. Water seepage may also be
a problem at the juncture of floor slab and walls. Use a liberal amount
of hydraulic cement to seal the area, and then smooth it with the trowel.
6. Applying Waterproofing Paint. Once the hydraulic cement
has cured and the wall is dry, use waterproofing paint to seal the walls.
Make sure the work area is well ventilated. For best results use a wide
nylon bristle brush to dab the mater al into the pores of the masonry.
Allow the first coat to dry overnight, and then apply a second coat.
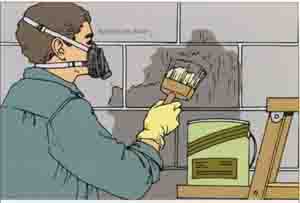
6. Use a wide nylon paintbrush to apply masonry waterproofer to the
walls. Work it into the rough surface of concrete block.
Correcting Severe Water Problems
If water continues to enter the basement despite efforts to seal the
walls from the inside, the problem must be tackled from the outside.
If an excessive amount of water builds up in the soil just outside the
foundation, it will be forced (by hydrostatic pressure) through the masonry.
Water that's under a modest amount of pressure can be sealed out with
waterproofing paint; however, large amounts of pressure can defeat any
product that's applied to the inside of the wall. A waterproofing layer that's applied to the outside of the foundation is far more effective.
This is because the more pressure is applied to it, the tighter the waterproofing
adheres to the wall. However, it’s not easy to waterproof the outside
of the foundation, and it’s expensive. Because all possible strategies
involve a good bit of excavation, this work is best left to a contractor.
The work typically involves digging down to the footing, installing a
system of drainpipes to redirect water around the house, and applying
a protective waterproofing membrane to the outside of foundation walls.
Compare several estimates before signing a contract.
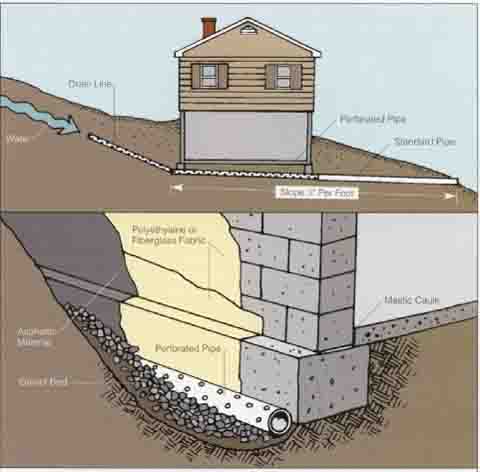
Correcting Severe Water Problems . Severe water problems can
be corrected by intercepting water before it reaches the foundation (top)
or by waterproofing the foundation itself (bottom), or both.
Sump Pumps
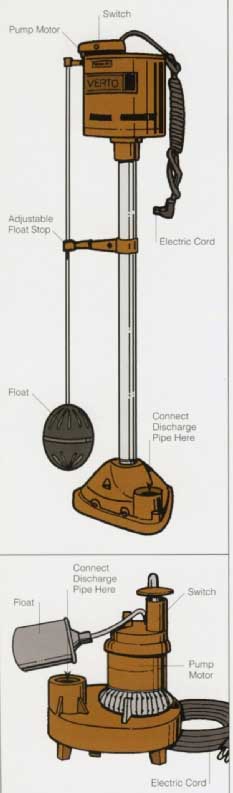
Types of Sump Pumps. The pump motor on a pedestal pump (top)
stays clear of the water. The pump motor on a submersible pump (bottom)
is immersed in the water.
One way to keep the basement dry is to install an electric sump pump.
This device draws water from beneath the slab and pumps it away from
the house. The pump sits in a hole, or sump, that extends below the slab.
When water collects in the sump, the pump turns on automatically and removes the water through a plastic discharge pipe that exits the basement
above grade.
The installation of a sump pump calls for wiring, plumbing, and concrete-
demolition skills. A pump must not be the only thing standing between
you and a flooded basement, however. After all, pumps do fail. A sump
pump may be part of a strategy to keep water out, but if water problems
are severe, footing drains may have to be installed as well.
Types of Sump Pumps. There are two basic types of sump pumps.
A pedestal-type pump features a raised motor that does not come in contact
with water. Instead, it sits on top of a plastic pipe that extends into
the sump. Water rising in the sump causes the float to rise and turn
on the pump. When the water level drops so does the float, turning off
the pump. With a submersible pump, the entire pump sits at the bottom
of the sump pit and is submerged every time the sump fills up with water.
A float on the pump triggers the on-off switch. Either type of sump pump
removes water effectively. Consult a plumber or a pump supplier to determine
the best one for your particular situation.
Installing a Sump Pump
In addition to plumbing codes, the pump installation must conform to
electrical codes, which in general terms means that the pump must be
supplied by a dedicated 15-amp circuit. The following step-by-step project
is a guide to how the work usually is done, but be sure to check local
codes and the manufacturer’s instructions that came with the pump. The
exact dimensions of the sump pit, For example, depend on the size of
the liner (sometimes called a basin). Purchase the pump and the liner
before starting work.
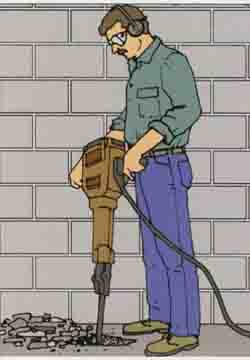
(24-1.jpg) 1. To reduce the amount of work involved in digging a sump,
rent a jackhammer, as shown, or a rotary hammer. Be sure to wear safety
glasses and hearing protection when using either tool.
1. Digging the Sump. The sump pump is located in the lowest
part of the basement so that water naturally drains to it. The whole
point of installing the device is to keep water out of the basement to
begin with, of course, but it’s still prudent to locate the pump this
way. Turn the basin upside down, and use it as a template to scribe a
circle on the floor; the circle’s centerpoint must be about 16 inches
away from both walls. Creating a hole in a 4-inch-thick slab is not easy
work, so rent an electric jackhammer or a heavy-duty rotary hammer for
the job. Wear safety glasses, and remove concrete up to the layout line.
Then dig out the soil and gravel beneath the slab—the depth depends on
the size of the liner (usually about 24 inches). Periodically slip the
liner into place to see if it fits.
2. Installing the Liner. The liner is a plastic tub with holes
in the sides that allow ground water to seep into it. Some liners have
a lip at the top that covers the edges of the concrete. Once the hole
is deep enough, slip the liner into place, fill in around it as needed
with gravel, and (if necessary) use hydraulic cement to seal the edges
of the hole.
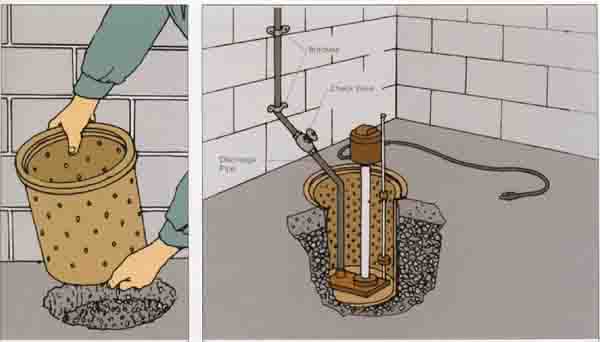
(25-0.jpg) 2. Slip the liner into place, and fill in with gravel
as needed; 3. The discharge pipe is usually PVC and must be secured
to the foundation walls with support clamps.
3. Connecting the Discharge Pipe. Check the manufacturer’s
instructions that came with the pump to determine the type of discharge
pipe needed and the necessary diameter (usually 1 7-inch PVC pipe). Attach
a piece of pipe that's long enough to reach the pump itself (submersible
type) or the intake housing (pedestal type). Then lower the pump into
the sump and connect additional discharge pipe as needed. Support clamps
must secure the pipe to the foundation walls, and a check valve must
be used somewhere in the discharge piping to keep water from draining
back into the sump. If the pump has to be removed for servicing, disconnect
the discharge pipe at the check valve. It usually has a threaded fitting.
4. Cutting the Rim Joist. It’s usually easiest to route the
discharge piping out through the rim joist. Afterwards, use caulk to
seal the hole. Be sure that the end of the discharge pipe does not dump
the water against the outside of the foundation walls. A splash block
can be used to direct water.

(25-1.jpg) 4. Cut a hole in the rim joist, and route the discharge
pipe through it. Direct water away from the foundation wall.
5. Wiring and Testing the Pump. Check local electrical codes
to see whether a ground-fault circuit interrupter (GFCI) is required
for a sump pump; then run wiring from the service panel to the general
location of the new pump. The pump itself has a long electrical cord and three-prong plug, so you must install a grounded receptacle for it.
This arrangement makes it easy to disconnect the pump should it ever
need servicing. The box is typically located high on a wall to avoid
splashes caused by the pump itself. (Check local codes for spe cifics.)
Use masonry anchors to secure a 2x4 to the foundation wall. (See page
36.) This provides a secure base for installing the electrical box. After
installing the discharge pipe, plug in the pump and pour water into the
sump. The pump begins to work when the sump is about half full. As water
flows through the discharge pipe, check all connections for leaks.
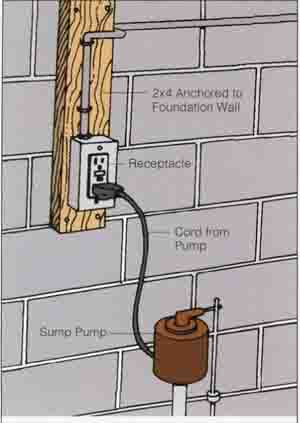
(26-0.jpg) 5. Use a 2x4, attached the foundation walls with masonry
anchors to create a base for installing the electrical box.
Basic Stair Dimensions
Your local building codes are the last word on stair dimensions but
the following can be a guide.
• The width of the stair must be at least 36 inches. Measure between
finished walls.
• Nosings (if used) must not project more than 1 1/2 inches.
• Headroom must measure at least 6 feet 8 inches from the tip of the
nosing to the nearest obstruction at all points on the stair.
• The ratio of riser height to tread depth should total 18 inches. The
ideal riser height, For example, is 7 inches and the ideal tread depth
is 11 inches (7 + 11 = 18). Risers must be no more than 8 1/4 inches
high; treads must be at least 9 inches deep.
• All stairs made up of three or more risers must have a 30- to 38-inch
handrail on at least one side. Handrails are measured vertically from
the tip of the tread nosing. The end of the handrail must return to the
wall or terminate hi a newel post.
• Landings must be the same width as the stair and at least as long
as they are wide.
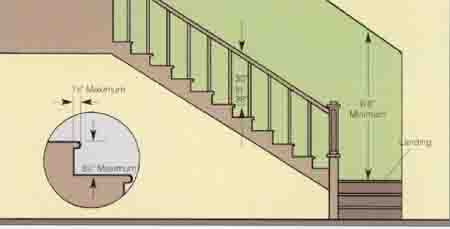
Stairs
One advantage to adding new living space in the basement rather than
the attic is that a stairway already is in place. It may be suitable
just the way it's , but in some cases it must be rebuilt. Building codes
are strict when it comes to stair construction, in part because small
variations in details such as step height make a big difference in the
safety of the stairs. For a basement conversion, you may decide to insulate
the concrete floor with a system of wood sleepers and rigid insulation
capped with plywood and carpeting. The thickness of this assembly changes
the height of the last step on the stairs; it becomes shorter than all
the others by the thickness of the new floor system. Unless this problem
is corrected, the stairs won’t be safe, and the project won’t pass code
inspection. Unfortunately, in this situation the stair carriage can't simply be raised—the stairs have to be rebuilt. There are other reasons
to rebuild a stairway, too. Though basement stairs in all newer houses
have to adhere to the same codes as those anywhere else in the house,
this was not always the case. If your house is an old one and the basement
stairs are uncomfortably steep or poorly constructed, they must be rebuilt.
This can usually be done without enlarging the stairwell itself. If it’s
necessary to build stairs, consult a reputable guide on stair building.
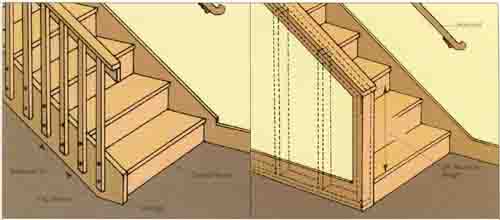
(27-0.jpg) Adding a Balustrade
Many existing basement stairs may not be up to code. In particular,
handrails and railings often are mis sing or inadequate. If the stairs
are usable otherwise, however, handrails can easily be added to an existing
stairway. Balusters are bolted directly to a stringer; bolts or screws
can be countersunk and concealed with wood plugs. Space the balusters
so that the opening between them is no more than 6 inches measured horizontally.
The top of the handrail must be easy to grasp.
Another option is to partly enclose the stairs on one side with a wall
that follows the stairway pitch. A handrail can be placed either on the
partial wall, on the full wall, or on both. The partial wall can be built
just as if it were a partition wall with a slanted top plate. The stringer
is securely fastened to the studs of the partition wall. Cover both sides
of the new wall with drywall or paneling.
Concealing Mechanical Equipment
A basement is packed with remodeling obstacles, including sump pumps,
water pumps, water heaters, pipes, ducts, drains, and furnaces, among
other things. It’s easiest to avoid these items from the start, so try
to work the design around them. If they can't be avoided, however, often
they can be concealed.
If the furnace shares space with basement living areas, safety is the
most important issue to consider. The furnace is best located in a separate
room, though it can share the space with other mechanical equipment such
as the water softener and water heater. Local building codes may regulate
the size and details of the room; check them for specifics. Generally,
however, a furnace room must have a door that's big enough to remove
the largest piece of equipment, though in no case can the door be less
than 20 inches wide. The room must contain an unobstructed working space
on the control side of the furnace that's at least 30 inches wide and 30 inches high. It’s also a good idea to provide a light that's controlled
by a switch near the door.
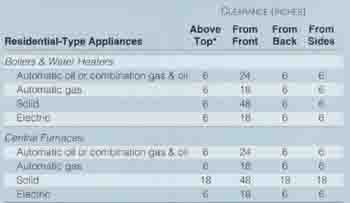
(27-1.jpg) Clearances For Heating Appliances
Be sure to vent the room so that there is enough incoming air for a
combustion-type furnace. The amount of air required depends on the type and capacity of the furnace; check with a local heating contractor.
As a safety precaution (particularly if someone is to sleep in the basement
even occasionally), install a carbon monoxide detector. Carbon monoxide
is a colorless, odorless, and potentially lethal gas that's a by-product
of combustion. Under normal circum stances carbon monoxide is vented
out of the house, but a faulty furnace or gas water heater may cause
it to leak into the basement. A detector sounds an alarm when it senses
car bon monoxide.
Building codes regulate the distance between heating appliances and combustible walls, so check local codes before building a room for the
furnaces and other appliances. In the meantime, however, the table “Clearances
For Heating Appliances” provides an idea of what is required.
Service Corridors. Combustion furnaces are supplied
with fuel via fuel lines. These fuel lines have a fuel filter that must
be accessible for periodic maintenance. Fuel lines must never run beneath
flooring but can be hidden behind a partition wall. By leaving about
24 inches between the partition wall and the foundation, a service corridor
is created and can be used for ready access to the line. A service corridor
also can be used to maintain access to other devices, such as a sump
pump or a water pump.
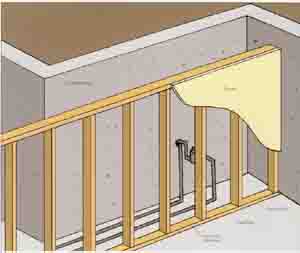
(28.jpg) Service Corridors. By leaving about 2 ft. of space between
a foundation wall and a partition, a service corridor is created and allows for easy access to various devices.
|