A continuous wall of concrete block resting on a footing of poured concrete
is the most expensive foundation for a vacation home and the hardest to build—but it's the strongest, the most permanent and the most weather-tight. It may
be required by a local building code; in any case it's generally necessary
for heavy buildings like log cabins, for maximum protection in earthquake
or hurricane country, and for unstable soil that can't support the pin-point
load of piers or poles. In other situations, the advantages outweigh the cost.
In very cold country, for example, concrete block is often preferred to elevated
foundations because it's easier to insulate and because a water heater and plumbing pipes can be housed in a weather-tight crawl space. The length of each wall in a block foundation must be a multiple of 8”—half
the length of a standard masonry block—or the walls will not fit together
properly. The footings must ex tend at least 18” below ground— more where
the frost line is deeper—and the walls must rise 24” above grade level,
to protect the wooden floor and walls from moisture and termites. To determine the number of blocks you need for the foundation walls, multiply
their total length in’ by the number of courses, then by .75. The mortar
can be made either from 1 part (by volume) portland cement, 1 part hydrated
lime, 6 parts damp sand, and water; or by combining 1 part premixed masonry
cement, 3 parts sand, and water.
If you need deep trenches for the footings, you probably will want to
get a backhoe operator to dig them for you; in any case, don't try to
dig deeper than 4’ unless you have had extensive experience that will enable
you to prevent dangerous cave-ins. Have dirt dumped just outside the trenches,
in low mounds that will not block the chute of a concrete truck; then,
after the floor joists are installed, you can backfill around the foundation
wall with the same dirt.
For a project of this size, it's usually easier to have the concrete
delivered in a transit-mix truck than to mix it yourself. Order one cubic
yard of concrete for every 22 linear ft. of footing. If possible, clear
the site so the truck can back up to each side of the building and pour
the concrete directly into the footings. Otherwise, assemble a group of
helpers with wheelbarrows and plywood chutes.
Planning and Pouring the Footing
1 Laying out the building lines. With stakes and two
steel tape measures lay out the outside of the foundation walls, using
the 3-4-5 triangle method to get right angles at the corners. Drive stakes
at two adjacent corners of the planned buildings, drive nails into the
tops of the stakes and stretch a string taut between the nails to indicate
one side of the building. Exactly 3’ along the string from one corner stake,
drive a measuring stake and nail. Have one helper hook a tape over that
stake, and a second helper hook a tape over the corner stake; swing the
tapes across each other. Where the 4-foot mark on the corner-stake tape and the 5-foot mark on the measuring-stake tape cross, drive another measuring
stake. Use this stake and the corner stake to establish the second side
of the building, measuring the length of the wall along a line running
through the two stakes and driving the third corner stake and its nail
at that point. Locate the fourth corner in the same way (inset), using
the previously established corner stakes and additional measuring stakes
to create a 3-4-5 right triangle (dashed lines).
For greater accuracy, you may prefer to use triangles based on multiples
of 3, 4 and 5’ — 9-12-15, for example. And to check your layout, compare
the diagonal measurements between corners, which should be identical.
2 Making and marking batter boards. Transfer the building
lines to structures called batter boards, which serve as reference points.
Drive three 2-by-4 batter-board stakes about 5’ out s de each corner stake
to form a right angle: matches the corner, then nail 1-by-6s 8 ft. long
to the three batter-board stakes. Stretch a string from a corner stake
to the batter boards at an adjacent corner and move the taut string until
it brushes the nail on top of the second corner stake, then mark the string’s
location on the top of the batter board. Repeat the procedure for the building
lines at each corner.
Mark each batter board, making the first mark 7 5/8” inside the building
line for the inside of the foundation wall; mark the board 4” outside the
building line and 12” inside for the footing. Mark an additional 24” outside
the outer footing mark and 6” inside the inner footing mark for the edges
of the trench (inset). Drive nails into the batter board at each mark and remove the corner stakes.
3 Digging the trench. Stretch strings between low stakes
driven at the trench-line marks and trace the strings along the ground
with a squeeze bottle of powdered chalk. Dig the trench to a depth 8” less
than the footing depth required by code. Caution: trenches deeper
than 4’ present a cave-in hazard and are best left to professionals.
Stretch strings between footing marks on the batter boards, drop plumb
lines from the strings to the bottom of the trench and mark lines for the
footing trench as you did for the original excavation. Dig the trenches
8” deep.
4 Leveling the footing trench. Drive 1-by-2 stakes at
each corner of the footing trench, mark one stake 8” from the bottom of
the trench and transfer the 8” mark to the other stakes with a water level.
For additional reference points, drive stakes 3” from the sides of the
trench every 3’, alternating from one side to the other, and transfer the
marks to them. Measure down from the mark on each stake to the bottom of
the trench and deepen it wherever necessary to at least 8”; the concrete
will fill any deeper sections.
Drive 16” lengths of ½” reinforcing bar— called grade pegs—into the footing
trench next to each stake until the top of each bar is level with the mark.
Remove the wooden stakes and tamp the dirt around the grade pegs.
5 Pouring a reinforced footing. Support long pieces of
No. 4 reinforcing bar about 3” above the bottom of the trench with bricks
or stones, then lash the bars to the grade pegs with wire. Where two pieces
of bar meet, overlap them about 16” and lash them together. To make bends
in the reinforcing bar for the corners, slip a piece of iron pipe over
the end of the bar, lay the bar on the ground, step on it and pull the
pipe up gradually.
Pour the concrete to just above the tops of the grade pegs and work it
around the reinforcing bars with a shovel, then level and smooth the concrete
with a wooden float until the tops of the grade pegs barely show. Cover
the footings with polyethylene sheeting and let them cure for at least
24 hours.
Stretch strings between the building-line marks on the batter boards,
drop a plumb bob from each string and snap matching chalk lines on the
footings. Remove the strings.
Lay four blocks on each side of the corner, checking them with the level
as you work; then spread a 1” bed of mortar on this course, set a corner
block on top of the first one and perpendicular to it, and tap the corner
block down. Check the height of the corner blocks with a story pole—a 1-by-2
marked every 8” to indicate the level of each course—building up or reducing
the thickness of the mortar joints as necessary.
Building the Foundation Wall
1 Building the leads. At each corner of the trench, lay
a stepped set of blocks called a lead. To start this part of the job, spread
a mortar bed 10” wide and 1½” thick from the corner, set a corner block
between the chalk lines and tap the block down with a trowel until the
mortar joint is 3/8” thick. Check the position of the block with a mason’s
level.
2 Leveling the wall. Hook a mason’s line between two
adjacent corners, using corner gripping mason’s blocks, and align the line
precisely with the top of the first course of blocks; then spread a 1½”
mortar bed on the footing and complete the first course of blocks. Keep
the face of each block 1/16” from the ma son’s line and the top level with
the line. When you reach the centers of the two opposite walls that will
support the girder—generally the shorter walls in a rectangular building—substitute
a solid block for the normal hollow-cored one. Move the mason’s line up
to lay the second and third courses, always using solid blocks where the
ends of the girder will rest. (In these pictures, solid blocks are indicated
by heavy outlines.)
Lay a mortar bed at each corner for the leads of the next three courses and press masonry-type wire-mesh reinforcement into the mortar, then lay
the next three courses. Add a layer of mesh reinforcement over every third
course.
3 Venting the crawl space. On opposite sides of the building,
about 4’ from the corners and 8” above ground, omit a block to leave a
space for a vent—one for every 300 square ft. of floor space. Fill around
the opening with mortar, set the vent 4” inside the wall, with its tabs
atop the blocks on either side, and pack mortar around the vent edges,
slanting mortar at the bottom outward to shed rain. In the next course,
use solid blocks over the vent.
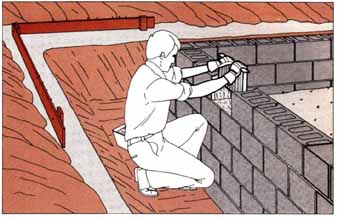
4 Making girder pockets. In the final course, insert
a partition block—a solid block 4 by 8 by 16”—at the center of each of
the girder walls. Set the block flush with the outside, leaving a 4”-deep
shelf inside for a pocket in which the girder will rest. Fill the cores
of all exposed blocks with mortar, troweling flush with the tops. Build
up the long walls, then proceed immediately to set anchor bolts (Step 5).
5 Setting anchor bolts. L-shaped anchor bolts, ½” thick and 8” long, are set into the mortar-filled cores a foot from each corner and every 4’ in between. To set each bolt, place it in a jig—a 1-foot 2-by-6
with a 3/8” hole through the center—attach its washer and nut, and place
the 2-by-6 flush with the out side of the block. Tap the anchor bolt into
the wet mortar until the washer lies flat against the 2- by-6. After 24
hours, remove the nuts and washers and slide the 2-by-6s off the anchor
bolts.
Supports for the Joists: Sills, Piers and Girder
1 Fastening the sill plate. Have a helper hold a section
of sill plate—a perfectly straight 2-by-6 pressure-treated with preservative—on
top of the final course of blocks with one end flush with the corner of
the wall and with one side touching the anchor bolts. With a framing square,
draw a line across the 2-by-6 at the center of each bolt; mark on each
line the distance from the wall edge to the bolt center and drill a ¾”
hole for each bolt. Fasten the sill plate over the bolts with their nuts and washers. Attach the remaining sections of sill plate and nail the ends
together. Cut 5¾-by-4” notches in the girder- wall plates over each pocket.
2 Laying out the piers. Drive nails partway into the
sill plates over the centers of the girder pockets and stretch a string
between the nails. Have a helper measure off one third and two thirds of
the distance between the outside edges of the foundation walls and mark
the string with cloth strips at these points.
Using a plumb line, locate and dig holes for pier footings below the strips,
excavating to the depth required by the local building code. Pour concrete
footings and set precast concrete piers or build masonry-block piers level
with the bottoms of the girder pockets.
3 Making and setting the girder. Cut three 2-by-8s 1”
shorter than the span between the backs of the girder pockets and fasten
them together with staggered 16-penny nails every 10”. With one helper
for every 5’ of girder length, set this girder in the girder pockets, leaving
½” of air space between the ends of the girder and the backs of the pockets.
Use steel plates or slate shims under the girder at the pockets and the
piers to bring the top of the girder flush with the top of the sill plate.
Cut several bricks in half and brick in the sides of the girder pocket,
using ¾” mortar joints between bricks and leaving ½” of air space on each
side of the girder.
If the span of the girder is longer than 16’, splice separate lengths
of 2-by-8. Stagger the splices and locate them directly above piers.
Constructing the Floor
1 Marking the sill plates for joists. Hook a tape measure—one
long enough to stretch the length of the wall—to a nail driven 15½” from
the end of a long wall and have a helper pull the tape taut. Set the tongue
of a framing square (the leg that's 1½” wide) across the plate at 16”
intervals, and draw lines on each side of the tongue. Mark the opposite
plate in the same way, starting at the same end of the building. To mark
the joist locations on the girder, stretch a chalk line between pairs of
marks on the two walls and snap the line over the girder.
2 Nailing header and stringer joists. Set a long, straight
2-by-10 on edge as a header joist—placing it flush with the outside of
the wall and parallel to the girder, and toenail it to the plate. Have
a helper butt another 2-by-10 (a stringer joist) against the first at the
corner, and nail the two boards together. Nail header and stringer joists
for the other two sides of the foundation wall in the same way, toenailing
them to the sill plate and to each other and butt-nailing them together
at the corners.
With a framing square, extend the lines that you marked for floor joists
in Step 1 onto the inside faces of the header joists.
3 Nailing the regular joists. Cut regular joists to fit
between the header joists and the center of the girder. Set two regular
joists in place between the header joists, lining them up with the marks
on the insides of the headers; drive three 16-penny nails through the headers
into the regular joists. Where the two regular joists meet, over the girder,
toenail them to the girder, then sandwich them between two 9¼” squares
of 3/8” plywood, nailed onto each side. Add a second pair of regular joists
in the same way.
4 Laying a vapor barrier. Unroll a length of 3-foot-wide
polyethylene sheeting over the crawl- space floor, beneath the two pairs
of joists; cut off the sheeting, and weight the corners with rocks. Then
nail in two more regular joists and unroll another length of sheeting,
overlapping the first by 6”; again weight it with stones. Continue nailing
joists, two at a time, and spreading polyethylene sheeting until you reach
the far end of the foundation.
5 Laying the subfloor. Add blocking between joists at
4-foot intervals to stabilize the joists and provide nailing surfaces for
plywood panels; toenail and face nail the blocking to the joists. Then
lay 3 exterior-grade plywood across the joists, and nail it down with eightpenny
nails; space the nails 6” apart across the ends of the panels and 10” apart
between ends. Stagger the end joints of the plywood panels, and leave gaps
between the panels, 1/8” at the ends and 1/16” along the sides.
- - - -
Where to Find Land
When America’s pioneers picked a spot for a cabin, they simply staked
out a land claim in the wilderness, sharpened their axes and went to work.
Putting up a cabin or cottage is more complex these days—and so is the
job of locating a suitable building site. But finding land is still a necessary
first step for a would-be cabin dweller: to move a project from the dream
stage to the drawing board, you must have your site picked out or purchased.
Obviously, land is generally cheaper and more readily available in regions
far from major metropolitan centers. But even in isolated areas, land prices
are rising along with demand. Americans are competing for rural property—particularly
for land near national or state parks, forests and recreation areas—and
landowners and real estate agents are well aware that this is so. Yet potential
land-buyer need not resign himself to paying an outrageous price for property.
There are still ways to find reasonably priced building sites, often without
giving up easy access to recreational areas.
One prime source of vacation land in the United States is a group of some
200 government projects west of the Mississippi. Initiated by the U.S.
Bureau of Reclamation, these projects generally begin with the damming
of a river, creating reservoirs with thousands of miles of new shoreline.
Most of these areas are supervised by the state agencies that cooperated
in their original planning and construction.
At some of these projects cabin- builders can lease small lots—the typical
size is a quarter acre. Leasing conditions and restrictions vary widely
from project to project and are subject to change, but when lots are available
they can be had for astonishingly low prices; in one recent year, for example,
lots were available at the Cedar Bluff and Lovewell Reservoirs in Kansas
at annual rents of less than $90 for a 25-year term. For the latest information
on the availability of such sites, apply to the appropriate state park
or recreation department, or to the administrator of a specific project.
Canadians can lease or buy recreational building lots on publicly owned
Crown lands. In recent years, for example, Ontario has made annual offerings,
in approved subdivisions, of hundreds of lots ranging from three quarters
to one acre. These properties are always advertised in the press, and are
later parceled out to potential buyers or renters in a public drawing.
If you can't lease or buy government land in the region you have picked
for your retreat, you must turn to the private market. For the quickest
in formation on where land is available— and at what price—start with the
most obvious sources: classified advertising listings in a metropolitan
newspaper in your chosen area, and the national or regional real estate
companies that publish periodic catalogues of country properties. But remember
that sellers of the remote parcels you are looking for don't advertise
widely. In general, only properties near recreational areas or major highways
turn up in the classified pages of major newspapers or the catalogues of
agents—and such land is nearly always the most expensive.
Once you have settled on a specific area, look for local sources of information
about land for sale. Subscribe to a leading small-town newspaper in the
locale you have chosen. These papers frequently carry land-for-sale advertisements
that don't appear in big-city newspapers or comprehensive catalogues.
They are also good sources of local political and economic news that might
affect land prices or influence your decision to buy. Plans for a major
new recreational area, for example, would increase the cost of property.
Another place to learn of land that may be up for sale is the tax assessor’s
office in the county you are considering. Tax records are open to the public, and if you can locate a parcel with a heavy bill for back taxes, you might
find that the owner would be willing to sell at a reasonable figure.
No matter where you decide to buy your land, there is no substitute for
firsthand inspection, and regular visits, to the area you have chosen can
often turn up a desirable building site. When ever you are in the area,
talk to country storekeepers and service-station operators—they often can
tell you of nearby landowners who might have property on the market.
You may, of course, decide that you want to build your cabin on private
land near a national or state park or recreation area, even though land
costs are likely to be higher than they would be for more remote sites.
If so, building sites can frequently be found either within or adjacent
to such lands, and you may be able to take advantage of a situation in
which private land is partly administered or protected by the government.
In New York State, for example, two huge preserves supervised by the state
have been set aside in the Adirondack and Catskill Mountains, and there
is a good deal of privately owned land available within these areas.
- - - - |